Результаты опытно-промышленных испытаний труб из высокопрочного чугуна с шаровидной формой графита (ВЧШГ) на объектах ООО «ЛУКОЙЛ-ПЕРМЬ»
В качестве материала стальных трубопроводов ООО «ЛУКОЙЛ-ПЕРМЬ» в основном применяются низкоуглеродистые стали (ст. 10, ст. 20), а также низколегированная сталь типа Г2С. Однако в последнее время заводы-изготовители трубной продукции все чаще предлагают использовать для строительства трубопроводов новые виды материалов с повышенной стойкостью к локальной коррозии, рассчитанные на работу в условиях высоких давлений (до 24 МПа) и низких температур (до -60°С). К таким материалам, в частности, относится высокопрочный чугун с шаровидной формой графита (ВЧШГ).
В 2009-2012 годах на Чураковском месторождении Компании были проведены испытания трубопроводов из ВЧШГ. По итогам 31 месяца эксплуатации наблюдалось замедление скорости коррозии за счет пассивации поверхности металла продуктами коррозии. Результаты ОПИ трубопровода, изготовленного из ВЧШГ, признаны положительными, в связи с чем в 2012 году на Москудьинском месторождении был введен в эксплуатацию нефтепровод из ВЧШГ.

На сегодняшний день общая протяженность трубопроводов различного назначения в ООО «ЛУКОЙЛ-ПЕРМЬ» составляет более 10 тыс. км (10464,14 км), из них на металлические трубопроводы приходится 8950,294 км (85,5%), неметаллические – 1513,846 км (14,5%). Максимальное количество отказов зафиксировано на металлических трубопроводах (рис. 1). Так, в 2014 году произошли 1232 отказа, из них 1092, или более 88% от общего количества, – отказы на стальных трубопроводах. Оставшиеся 12% (104 отказа) приходятся на коррозионно-стойкие трубы: со стеклоэмалевым покрытием, трубы стеклопластиковые комбинированные (ТСК), ТСТ и КСР (коррозионно-стойкий рукав). Если рассматривать отказы по назначению трубопроводов, то складывается следующая картина: 550 отказов (44,6 %) произошли на нефтепроводах, 609 (49,4%) – на водоводах и 36 (3%) – на газопроводах. Порядка 823 отказов произошли на трубах со сроком эксплуатации более 20 лет.
Основной причиной отказов металлических труб остается наружная и внутренняя коррозия. В случае неметаллических – заводской и строительный брак, «хождение» грунтов, повреждения в результате внешнего воздействия (человеческий фактор).
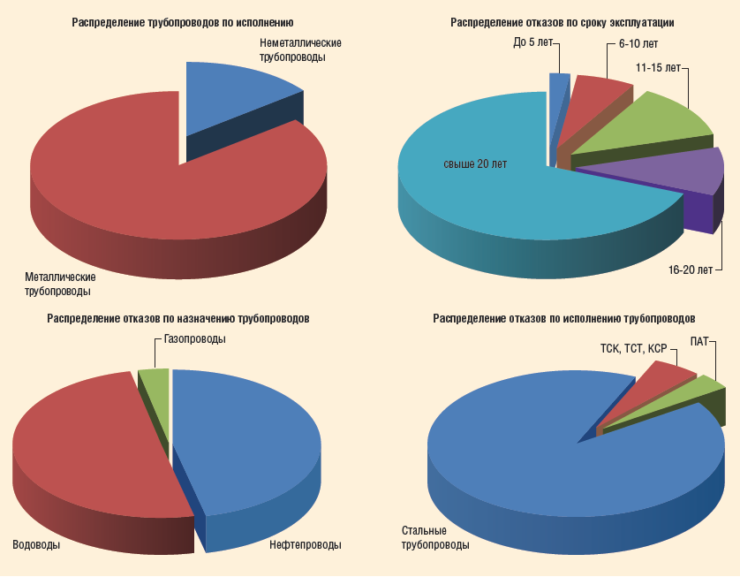
В качестве материала стальных трубопроводов чаще всего используются низкоуглеродистые стали – ст. 10, ст. 20 и, реже, низколегированная сталь (типа Г2С). Между тем, заводы-изготовители трубной продукции разработали и предлагают новые материалы с повышенной стойкостью к локальной коррозии, способные выдерживать высокие давления (до 24 МПа) и работать при низких температурах (до -60°С), в том числе и такой необычный для нефтяной промышленности материал, как высокопрочный чугун с шаровидной формой графита.
В рамках ОПИ для оценки возможности применения труб из ВЧШГ на объектах ООО «ЛУКОЙЛ-ПЕРМЬ» в 2009 году был произведен монтаж участка нефтепровода Чураковского месторождения. В проекте использовались трубы диаметром 80 мм и толщиной стенки 6 мм. Рабочее давление в нефтепроводе составляло 3,2 МПа, протяженность участка – 160 м (рис. 2). Трубы были изготовлены ОАО «Свободный Сокол» и поставлены дочерним предприятием ООО «ПКФ «Малый Сок». Продолжительность ОПИ составила 31 месяц, съем образцов производился через 9, 18 и 31 месяц эксплуатации. Нефтепровод смонтировали специалисты ООО «ПКФ «Малый Сок».
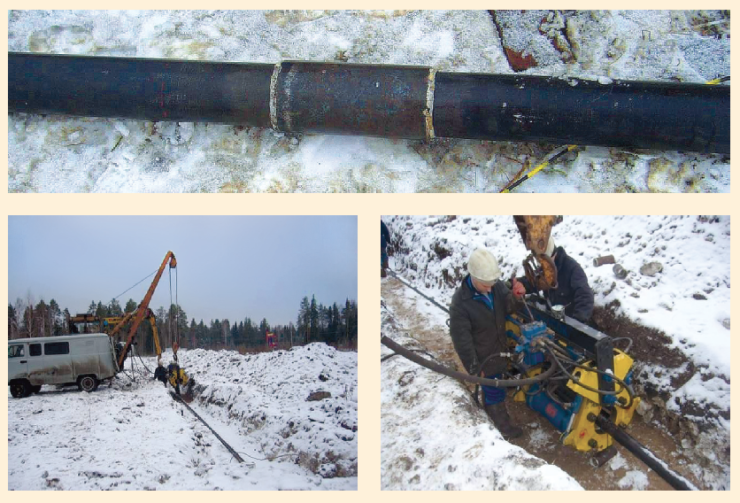
Попутно добываемая вода, транспортируемая через данный нефтепровод, представляет собой рассол хлоркальциевого типа с большим содержанием солей – до 257 г/л. Сероводород и кислород в воде отсутствуют, но отмечается наличие углекислоты на уровне 37 мг/л. Расчет стабильности воды, то есть способности ее к выделению взвесей и осадков, показал, что даже при температуре от 10 до 20°С вода нестабильна по карбонатам (ПС>1), и высока вероятность образования солевых отложений на поверхности работающего оборудования и трубопроводов. Присутствие отложений может провоцировать усиление локальных коррозионных процессов за счет протекания так называемой подосадковой коррозии.
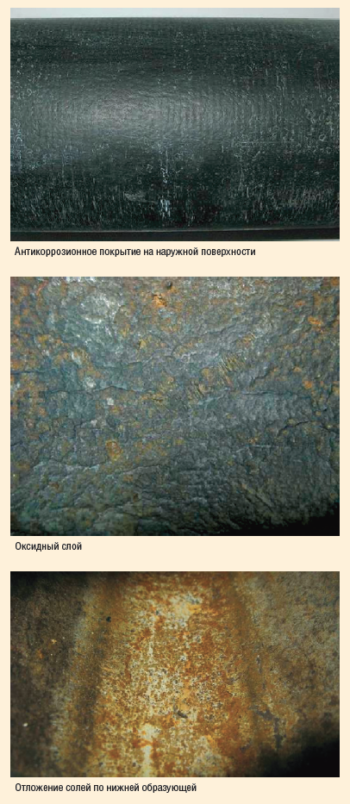
в течение девяти месяцев
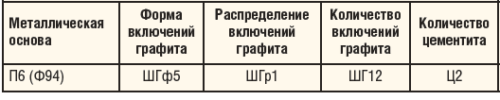
ИССЛЕДОВАНИЯ ПОСЛЕ ДЕВЯТИ МЕСЯЦЕВ ЭКСПЛУАТАЦИИ
Для оценки состояния трубы через девять месяцев эксплуатации вырезанный фрагмент трубопровода направили в отдел защиты от коррозии филиала ООО «ЛУКОЙЛ-Инжиниринг» «ПермНИПИнефть» в г. Перми для проведения исследований. Анализ состояния трубы показал, что на наружной поверхности присутствовало темное защитное антикоррозионное покрытие, механических повреждений покрытия до металлической основы обнаружено не было (рис. 3). Внутренняя поверхность трубы темная, шероховатая, ячеистая.
На нижней образующей присутствовал слой солевых отложений, представленных карбонатом кальция, АСПО отсутствовали. Продуктов коррозии и очагов коррозионного поражения в виде язв и питтингов даже под слоем солей обнаружено не было.
Методом металлографического анализа установлено, что структура чугуна представлена ферритной основой с включениями перлита и графита (рис. 4). Все параметры структуры высокопрочного чугуна определялись в соответствии с ГОСТ 3443 и приведены в табл. 1. Количество перлитной составляющей соответствовало П6 (Ф94), форма графитовых включений правильная, шаровидная (ШГф5), распределение включений графита по толщине стенки трубы равномерное (ШГр1), количество графита составило 12% (ШГ12), доля цементита не превышала 2% (Ц2).
На наружной поверхности трубы присутствовало защитное антикоррозионное покрытие толщиной 260 мкм, состоявшее из темного слоя битумного лака, светло-серого промежуточного слоя цинкового покрытия толщиной около 40 мкм и темно-серого слоя, прилегавшего к основе, толщиной около 25 мкм (структурная составляющая трубы), обусловленного технологией изготовления (центробежное литье) и представленного оксидом железа.
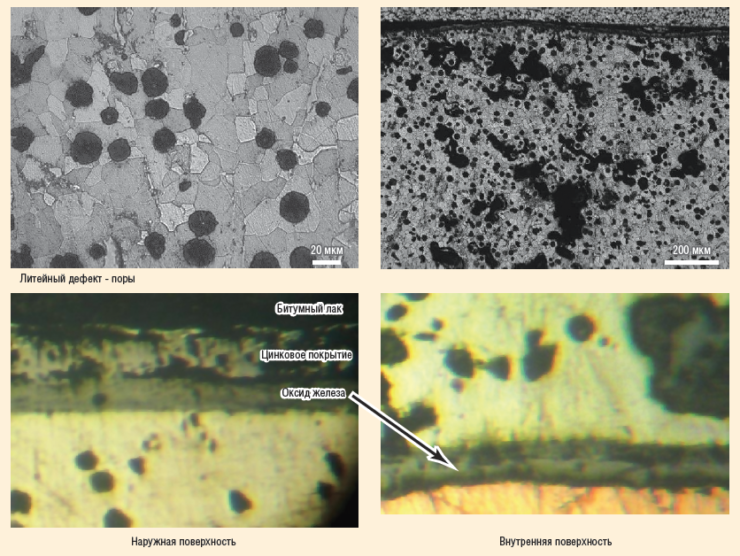
На внутренней поверхности трубы наблюдался литейный дефект в виде пор на глубину до 1,2 мм. Согласно требованиям ТУ на наружной и внутренней поверхностях труб допускаются пороки, обусловленные способом производства и не влияющие на герметичность труб при гидравлическом испытании.

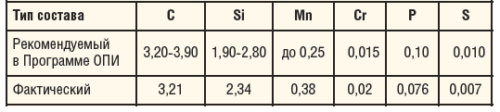
Для оценки соответствия материала трубы нормативным значениям были определены механические свойства трубы, которые удовлетворяли требованиям ТУ и химический состав (табл. 2, 3). Химический состав в ТУ не регламентировался, поэтому его сравнивали с приведенным в программе ОПИ. Было обнаружено завышение содержания марганца, содержание остальных элементов соответствовало рекомендуемому составу.
ИССЛЕДОВАНИЯ ПОСЛЕ 18 МЕСЯЦЕВ ЭКСПЛУАТАЦИИ
Второй съем образцов произвели через 18 месяцев эксплуатации. Для проведения исследований был выбран фрагмент трубы с муфтовым соединением (рис. 5). Анализ состояния трубы показал, что после 18 месяцев эксплуатации произошло частичное выкрашивание битумного лака с наружной поверхности; в муфтовом соединении с обеих сторон идентифицирован эпоксидный клей.
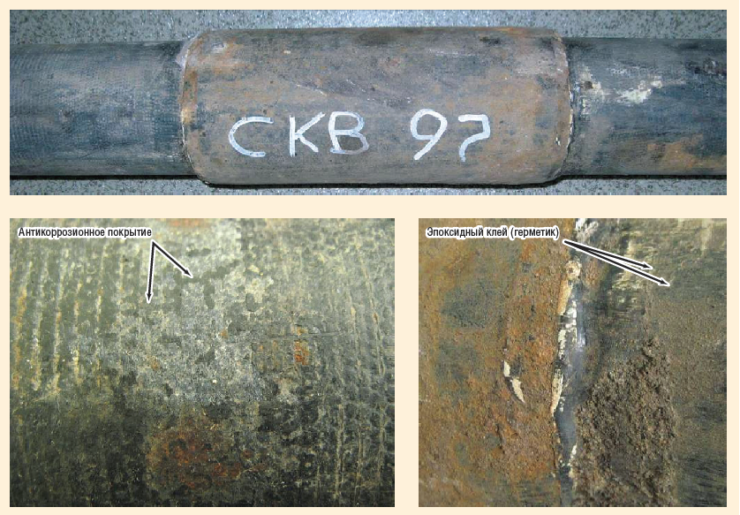
Внутренняя поверхность трубы по нижней образующей характеризовалась вздутием и отслаиванием карбонатов и внутреннего оксидного слоя трубы, наличие которого обусловлено технологией изготовления (рис.6). В месте отслаивания оксидного слоя образовались коррозионные язвы глубиной до 450 мкм. На участке стыка труб присутствовал эпоксидный клей, полностью изолировавший муфту от транспортируемой жидкости. Учитывая, что муфта была выполнена из стали 20, это можно отнести к положительным аспектам эксплуатации.

В месте присутствия пор, представляющих литейный дефект и допускаемых ТУ, наблюдалось коррозионное поражение основы на глубину формирования пор – 1,7 мм (рис. 7). Присутствие пор в структуре трубы отрицательно повлияло на ее коррозионную стойкость. Для изоляции пористости завод-изготовитель по требованию заказчика может поставлять трубы сцементно-песчаным покрытием (ЦПП) или с полиэтиленовой пленкой (рукавом).
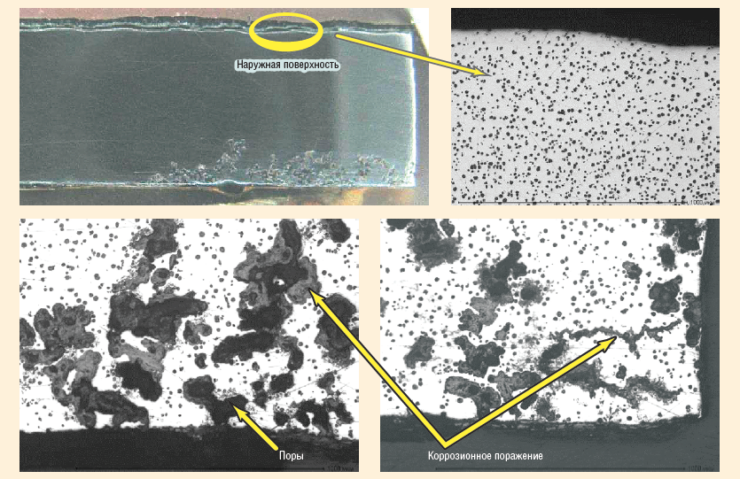
На наружной поверхности трубы коррозионных поражений обнаружено не было. Это обусловлено наличием цинкового покрытия, выполняющего функцию протекторной защиты, что подтверждено отсутствием следов коррозии в местах удаления битумного лака.
ИССЛЕДОВАНИЯ ПОСЛЕ 31 МЕСЯЦА ЭКСПЛУАТАЦИИ
Анализ состояния трубы после 31 месяца эксплуатации показал, что состояние внутренней и наружной поверхностей по сравнению с состоянием трубы после 18 месяцев эксплуатации практически не изменилось: наблюдалось вздутие и отслаивание карбонатов и внутреннего оксидного слоя трубы (рис. 8). По верхней образующей трубы уже наблюдалось отложение нефтепродуктов, что было обусловлено высокой шероховатостью внутренней поверхности трубы.
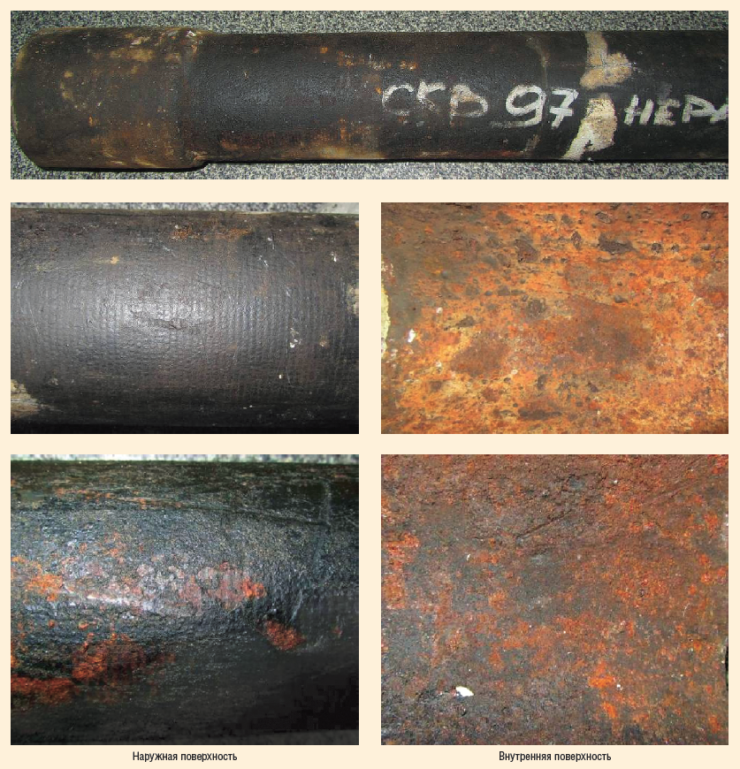
Сама внутренняя поверхность трубы подверглась коррозионному поражению с образованием коррозионных язв глубиной до 100 мкм. Также здесь присутствовал литейный дефект в виде пор на глубину до 0,2 мм. Наблюдалось замедление коррозионного процесса (рис. 9).
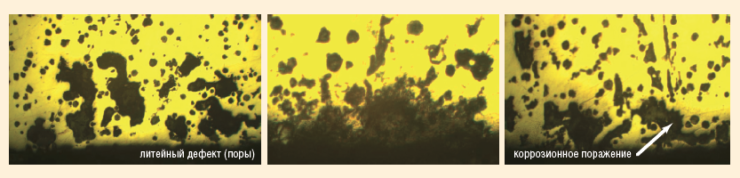
РЕЗУЛЬТАТЫ ОПИ
В целом результаты ОПИ изготовленного из ВЧШГ трубопровода признаны положительными. После трех лет эксплуатации наблюдалось замедление скорости коррозии за счет пассивации поверхности металла продуктами коррозии. Скорость коррозии трубопровода составила 0,038 мм/год. По результатам ОПИ в 2012 году на Москудьинском месторождении был введен в эксплуатацию нефтепровод из ВЧШГ протяженностью 5,125 км.
Следует отметить, что при вводе нефтепровода в эксплуатацию возник ряд осложнений (рис. 10). В частности, были зафиксированы два отказа по причине разрушения трубы по телу при проведении очистки полости трубопровода воздухом с пропуском очистных устройств (полиуретанового шара, поролонового поршня). Также были обнаружены малая толщина стенки и механическое повреждение при проведении монтажных работ. Наблюдались многочисленные отказы по причине нарушения герметичности неразъемного муфтового соединения при повышении давления.
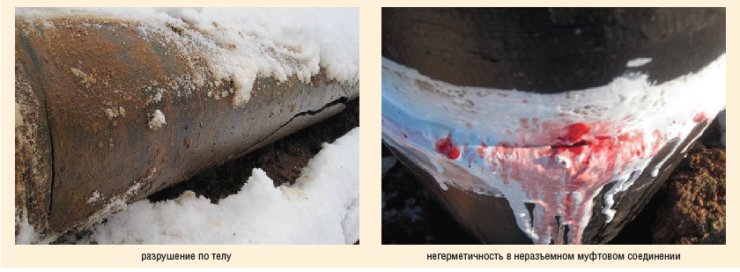
В итоге было принято решение о замене труб с неразъемным соединением на трубы с раструбным соединением типа RJ. После замены труб был зафиксирован один отказ по причине негерметичности раструбного соединения типа RJ.
После ввода в эксплуатацию в 2012 году ни одного отказа на данном участке нефтепровода не зафиксировано, как и на участке нефтепровода из ВЧШГ, смонтированного на Чураковском месторождении.
Для отправки комментария вам необходимо авторизоваться.