Основные итоги и задачи в области повышения надежности УЭЦН
Почти пять лет назад ТНК-ВР взяла стратегический курс на двукратное повышение наработки на отказ УЭЦН к концу 2011 года. Сегодня Компания стоитна пороге реализации Стратегии и достижения показателя наработки 600 суток.
Ключевым фактором успеха стала последовательная, методичная аналитическая работа с фондом УЭЦН, основанная на научно-исследовательской программе, скрупулезном изучении статистики и структуры отказов, а также взаимодействии с заводами и сервисными предприятиями.
В то же время, приближаясь к достижению поставленной цели, специалисты ТНК-ВР все чаще задумываются: возможен ли дальнейший рост этого показателя, и если да, то насколько? Определение технически и экономически обоснованных уровней наработки по каждому предприятию Компании является важной частью реализации новой Стратегии повышения эффективности механизированной добычи.
СТРАТЕГИЯ ПОВЫШЕНИЯ НАРАБОТКИ НА ОТКАЗ УЭЦН
В 2003–2006 годах средняя наработка на отказ скважин, эксплуатируемых УЭЦН, в компании ТНКBP составляла 300 суток. Такой невысокий показатель негативно влиял на эксплуатационные и капитальные затраты на добычу нефти, и совет директоров Компании в июле 2006 года принял стратегию по увеличению наработки на отказ УЭЦН до 600 суток к концу 2011 года. Экономический эффект от реализации принятой стратегии (NPV) в горизонте пяти лет оценивался на уровне $340 млн, в долгосрочной перспективе 20 лет – более $1 млрд.
Таким образом, за пять лет нам предстояло фактически удвоить продолжительность безотказной работы погружного оборудования.
В начале 2007 года была разработана общая концепция реализации Стратегии повышения наработки на отказ УЭЦН. В ней были обозначены основополагающие условия и приоритетные пути достижения целей Стратегии (рис. 1).
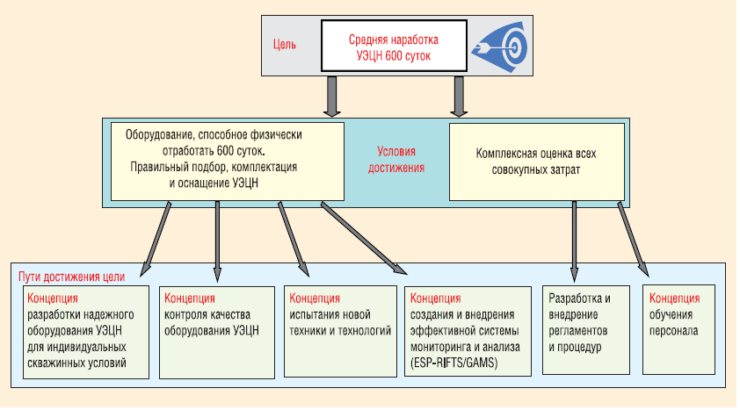
Во-первых, это применение надежного оборудования, физически способного отработать 600 суток. Во-вторых, создание благоприятных условий работы этого оборудования: устранение всех факторов и осложнений, не позволяющих оборудованию выработать свой ресурс. И, в-третьих, предотвращение нарушений на всех этапах жизненного цикла УЭЦН.
При этом всю работу было решено разделить на несколько наиболее приоритетных направлений действий:
- разработка надежного оборудования для индивидуальных скважинных условий;
- внедрение контроля качества нового оборудования и качества ремонта оборудования;
- внедрение эффективной схемы испытания новой техники и технологий;
- создание и внедрение системы мониторинга и анализа работы механизированного фонда;
- разработка и внедрение регламентов и процедур применения УЭЦН, а также системы обучения персонала.
Тогда же, в 2007 году, по каждому из обозначенных направлений действий были разработаны программы работ, состоящие из адресных мероприятий по каждому добывающему обществу и в целом по Бизнес-направлению. В последующие периоды был организован процесс формирования ежегодных программ работ, основанный на анализе результатов, полученного опыта и извлеченных уроках за прошедшие периоды, технико-экономической оценке эффективности планируемых мероприятий.
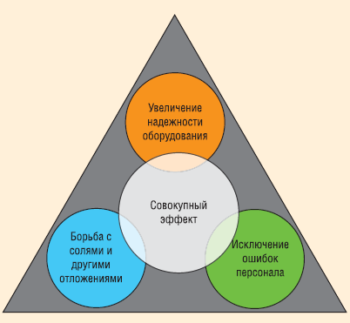
БАЗОВЫЕ ПРИНЦИПЫ
Принципы и подходы, которыми мы руководствовались в самом начале проекта, не утратили актуальность и в настоящее время.
Прежде всего успех реализации Стратегии базируется на синергетическом эффекте от трех составных частей – применении надежного оборудования, борьбе с осложнениями и исключении ошибок персонала на всех этапах применения оборудования (рис. 2).
Применяемая идеология: «Нецелесообразно приобретать дорогое оборудование с повышенным ресурсом, не решив проблему ранних отказов и проблему солеотложения. И, наоборот, нет смысла тратить средства на защиту от солей, если в скважине эксплуатируется оборудование с низким ресурсом. Максимальный эффект достигается только тогда, когда применяется комплексный подход».
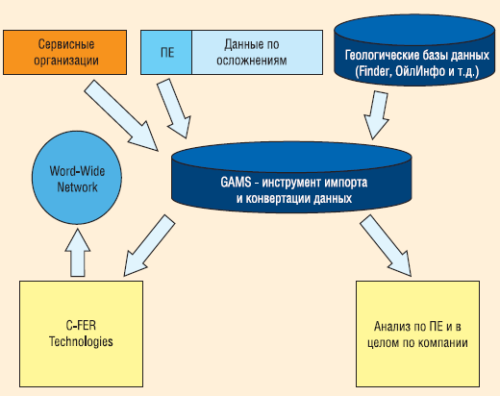
МОНИТОРИНГ И АНАЛИЗ
Одна из первоочередных задач, которая была решена в самом начале пути, – внедрение системы мониторинга и анализа ESP-RIFTS (Electric Submersible Pump Reliability Information Failure Tracking System) и создание корпоративной Системы группового анализа и мониторинга GAMS (Group Analysis Monitoring System) (рис. 3). Это ключевой инструмент, при помощи которого нам удалось решить целый набор задач в рамках реализации стратегии повышения наработки на отказ. Во-первых, система позволяет определять основные проблемы, причины и факторы, влияющие на уровень отказов УЭЦН. Во-вторых, это возможность выявления как надежного и эффективного оборудования, так и ненадежного и неэффективного. В-третьих, система позволяет определять слабые места в системе УЭЦН в различных скважинных условиях, внося соответствующие изменения в Технические требования к оборудованию. И, наконец, это определение лучших технологий и практик, в том числе с оценкой эффективности внедрения новых технологий в области эксплуатации УЭЦН.
Внедрение системы мониторинга и анализа началось с разработки единой теоретической базы, терминологии и подходов (процедура расследования отказов УЭЦН, стандарт отказов, справочники, классификаторы, форматы и т.д.). Далее мы сформировали массив достоверных данных по всем скважинам Компании и отказам УЭЦН.
В августе 2008 года был разработан формат «Комплексного анализа отказов УЭЦН» с периодичностью подготовки отчета раз в полугодие.
В итоге именно применение инструментов системного анализа позволило выявить первостепенные причины и факторы, сдерживающие рост наработки на отказ в условиях различных месторождений нефти, и сформировать на основе этого адресные программы мероприятий, направленные на устранение этих причин и факторов.
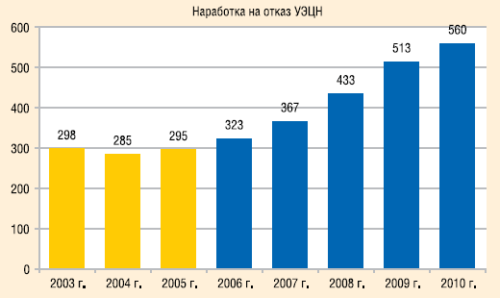
Интегральным показателем успеха проводимой работы служат прежде всего показатели наработки на отказ УЭЦН в скважинах Компании. Именно поэтому устойчивый рост наработки УЭЦН во всех дочерних обществах (ЦДО) ТНК-ВР в 2006–2010 годах можно с уверенностью назвать динамикой «достижений» Компании и ее партнеров в деле реализации принятой Стратегии. На 1 января 2011 года наработка УЭЦН составила 560 суток (рис. 4). Но специалисты ТНК-ВР считают, что останавливаться на достигнутом еще рано.
Кроме наработки на отказ на уровень затрат на эксплуатацию скважин механизированного фонда влияет и такой фактор, как частота проведения геолого-технических мероприятий (ГТМ). Поэтому с 2011 года для оценки эффективности работы механизированного фонда Компания использует новый показатель среднего времени работы скважин до остановки за скользящий год с учетом ГТМ.
АНАЛИЗ ОТКАЗОВ
Результаты анализа отказов УЭЦН однозначно говорят о том, что на протяжении последних пяти лет самым слабым узлом системы был и остается насос. Вторым по значимости за ЭЦН следует кабель. Между тем, несмотря на то что доля отказов по данным узлам остается высокой, удельный уровень отказов по насосам снизился в два раза, по кабелю – в полтора раза. С работой по повышению надежности этих двух узлов УЭЦН мы и связываем основные успехи работы по повышению наработки на отказ за прошедшее время.
Отказ от применения насосов «первой группы» с рабочими ступенями (РС) из серого чугуна способствовал повышению надежности узла «насос» и УЭЦН в целом. Однако существенного перераспределения отказов по другим узлам не произошло. Это может свидетельствовать о том, что гипотеза о независимости вероятностей наступления отказов отдельных узлов, применяемая в методах математической статистики, не совсем корректна.
Таким образом, основным ресурсоопределяющим элементом системы УЭЦН в ТНК-ВР является насос, вне зависимости от достигнутого показателя наработки на отказ. Поэтому большой потенциал дальнейшего повышения эффективности механизированной добычи по-прежнему заключается в снижении отказов по причине засорения насосов и повышении износостойкости ЭЦН.
НАУЧНО-ИССЛЕДОВАТЕЛЬСКИЕ РАБОТЫ ПО ПОВЫШЕНИЮ НАДЕЖНОСТИ УЭЦН
Как сказано выше, еще в 2007 году в ТНК-ВР была сформулирована Концепция разработки надежного оборудования (УЭЦН) для индивидуальных скважинных условий. Это прежде всего научно-исследовательские работы, цель которых состоит в получении научно обоснованных рекомендаций по повышению надежности насосных секций и узлов УЭЦН на основе исследования физики отказов и механизмов разрушений. Работа ведется Компанией совместно с сотрудниками Института машиноведения им. А.А. Благонравова РАН и ООО «ИМАШ ресурс».
Методология работ основывается на анализе статистических данных, исследовании основных процессов разрушения деталей и узлов УЭЦН, физики отказов. Это позволяет выделять ресурсоопределяющие узлы и детали УЭЦН, то есть узлы, становящиеся первопричиной отказов установки.
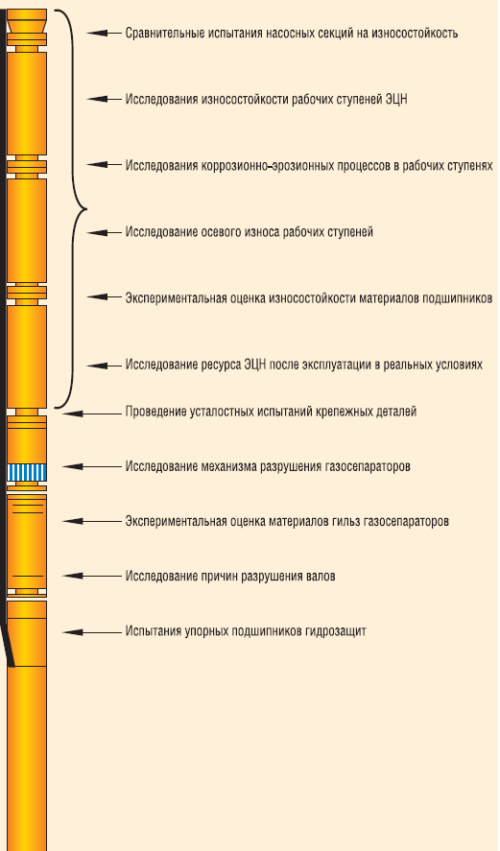
В рамках этого же направления разработаны методики испытаний на основе принципа автомодельности (подобия), оригинальные стенды и проведены сравнительные испытания ресурсоопределяющих деталей. Общая структура работ представлена на рис. 5. Учитывая, что основным ресурсоопределяющим элементом системы УЭЦН в ТНК-ВР является насос, главный акцент в научной работе был сделан на исследованиях, направленных прежде всего на повышение надежности ЭЦН.
В ходе научно-исследовательских работ удалось выявить фундаментальные закономерности динамики изнашивания узлов ЭЦН, исследовать триботехнические характеристики применяемых материалов РС, подшипников, влияние на ресурс конструкции насоса и т.д. Полученные данные, в свою очередь, позволяют определять критерии работоспособности и допустимые скорости изнашивания РС для заданных условий эксплуатации, а также прогнозировать ресурс насоса (определять технические пределы срока работы различных конструкций ЭЦН в конкретных скважинах).
Вся эта работа в итоге трансформируется в выработку конструктивных решений по повышению надежности оборудования и обоснованное повышение уровня технических требований к новому и ремонтному оборудованию. К сегодняшнему моменту проведена довольно масштабная работа, которая уже приносит Компании огромную практическую пользу.
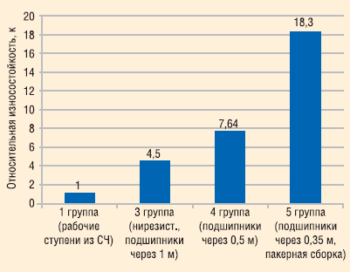
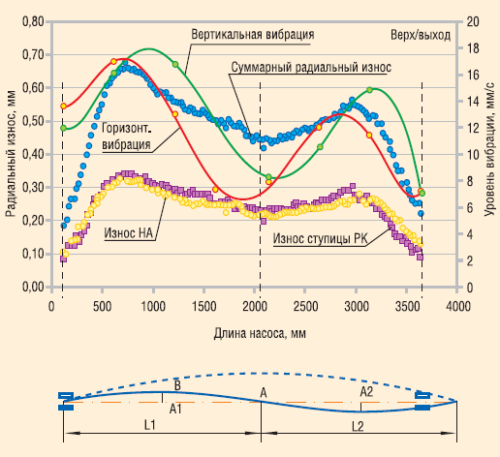
По результатам стендовых испытаний насосных секций была выполнена оценка влияния конструктивного исполнения насосов на износостойкость.Мы видим, что насосы первой группы исполнения уступают насосам третьей группы по износостойкости в 4,5 раза (рис. 6).
Четвертая группа, в которой подшипники установлены через полметра, имеет практически в два раза большую износостойкость по сравнению с третьей группой. Пятая группа в условиях стенда показывает в четыре раза большую износостойкость по сравнению с третьей группой.
Установлено, что величина износа радиальных сопряжений РС непосредственно влияет на вибрацию насосной секции, определяет вероятность наступления отказа функционирования УЭЦН. В процессе изнашивания возникают поперечные колебания, создающие в элементах корпуса знакопеременные напряжения. Как видно из рис. 7, существует корреляция между износом радиальных сопряжений и виброскоростью. То есть по величине виброскорости при использовании ТМС можно судить о степени износа радиальных сопряжений РС и более обоснованно назначать уставки по вибрации.
Максимальная величина износа радиальных сопряжений РС при использовании промежуточных подшипников ограничивается стрелой прогиба участка вала между ними. Таким образом, расстояние между промежуточными подшипниками определяет износостойкость РС. Это, однако, справедливо, если промежуточные подшипники изготовлены из высокоизносостойких материалов, например твердых сплавов, и имеют достаточную ударную вязкость. Полученные результаты позволили усовершенствовать технические требования к ЭЦН (в новых технических требованиях редакции 2009 года добавлены новые группы 4А и 5А). Таким образом, оптимизировав расположение промежуточных подшипников с учетом эксплуатационных условий и вибропараметров, мы добились качественного повышения надежности («технического предела») насосных секций.
Была проведена целая серия экспериментов по измерению осевых сил и исследованию износостойкости осевых сопряжений РС различных заводов (различных конструкций) одного типоразмера (рис. 8). На специально разработанном стенде мы проводили измерение нагрузок, действующих на шайбу колеса, в различных точках напорно-расходной характеристики ступени. В результате исследований было установлено, что рабочие ступени существенно различаются по величине осевой силы, что обусловлено непосредственно конструкцией РС (осевую силу отличает двойственность природы: она зависит как от конструктивных особенностей РС, так и от рабочей точки напорно-расходной характеристики).
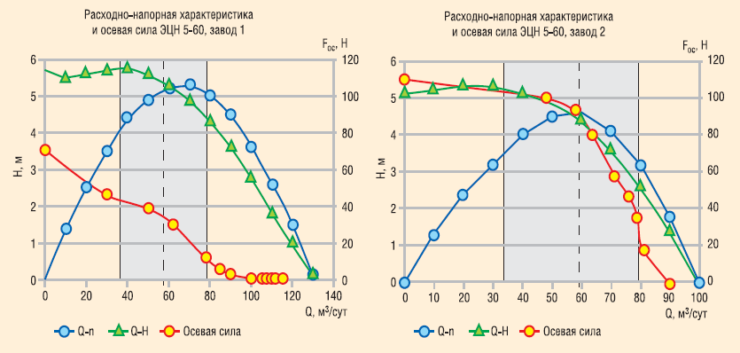
В свою очередь, износостойкость осевых сопряжений РС самым непосредственным образом зависит от величины удельной осевой нагрузки: чем выше нагрузка, тем больше скорость изнашивания – зависимость имеет практически линейный характер. Поэтому при конструировании РС величина осевой силы (удельной осевой нагрузки на шайбу колеса) должна приводиться наряду с напорно-расходной характеристикой в технической документации (требование включено в Технические требования к ЭЦН редакции 2009 года).
МОДЕЛИРОВАНИЕ ПРОЦЕССА РАЗРУШЕНИЯ «ПРОМЫВ»
«Промыв» материала РС, корпуса ЭЦН, входного модуля, газосепаратора приводит к наступлению аварийной ситуации, отказу функционирования. Необходимо было понять физическую природу этого явления на фоне имевшихся противоречивых сведений. Например, «промыв» РС имел место при незначительном износе сопряжений или более твердые материалы РС «промывались» более интенсивно, чем менее твердые, что не соответствует гипотезе определяющего влияния абразива на этот процесс разрушения.
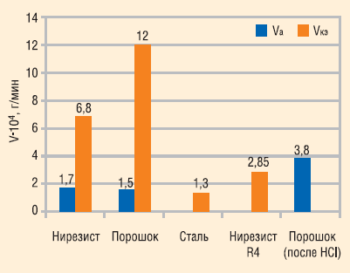
При проведении испытаний РС на изнашивание было исследовано влияние основных осложняющих факторов: абразива и коррозионно-активной жидкости. В результате удалось по-новому взглянуть на применяемые материалы РС и газосепараторов, поновому их классифицировать. Было выявлено, что порошковые материалы, за исключением высоколегированных, не уступая нирезисту по износостойкости в абразивосодержащей среде, при испытаниях в абразивосодержащей, коррозионно-активной среде резко ее теряют (рис. 9). Полученные результаты легли в основу новых технических требований ТНКВР к ЭЦН (пересмотрены требования к материалам для 2, 4, 5, 4А и 5А групп ЭЦН).
В ходе этой работы была впервые разработана понятная модель отказа («промыв») и методика испытаний материалов. Физическая природа «промыва», по мнению специалистов, заключается в воздействии на поверхность детали вихреобразного потока абразивосодержащей коррозионно-активной жидкости. На испытательном стенде был воспроизведен «промыв» РС в соответствующей зоне и соответствующей формы, что подтверждает принцип автомодельности опыта.
ОПРЕДЕЛЕНИЕ «ТЕХНИЧЕСКИХ ПРЕДЕЛОВ» УЭЦН
Мы стоим на пороге реализации Стратегии повышения наработки на отказ УЭЦН и достижения показателя наработки 600 суток. Поэтому разумен вопрос: а что дальше? Какой уровень наработки будет технически и экономически оправдан?
Одна из главных задач, решаемых в ходе реализации Стратегии повышения эффективности механизированной добычи нефти, – это определение технически и экономически обоснованных уровней наработки по каждому ЦДО, по каждому объекту разработки в зависимости от специфики скважинных условий и уровня развития технологий. Для решения данной задачи необходимо иметь четкое понимание технических пределов срока работы различных конструкций УЭЦН в зависимости от условий эксплуатации.
Как было отмечено выше, основной ресурсоопределяющий элемент системы УЭЦН в ТНК-ВР – это насос, представляющий сложную трибологическую систему, подверженную различным видам изнашивания. Поэтому ресурс (технический предел) насоса прежде всего определяется скоростью развития процессов разрушения и предельным состоянием радиальных, осевых сопряжений и деталей, подверженных «промыву», которое в свою очередь зависит от условий наступления параметрического отказа и отказа функционирования.
Важным этапом исследований по определению технических пределов работы оборудования стала работа по послеэксплуатационному анализу УЭЦН. В течение трех последних лет по специально разработанной методике послеэксплуатационного анализа насосных секций (методика в настоящее время является приложением к техническим требованиям на ремонт оборудования) проводилось измерение износа 90 насосов (более 200 насосных секций) и анализ эксплуатационных условий.
Суть подхода к определению ресурса, или технического предела, заключается в следующем. Зная срок работы оборудования в скважине, зная величину износа ступеней, мы определяем скорость изнашивания. На основании этой величины, ориентируясь на предельное значение состояния по износу как для осевых, так и радиальных сопряжений, мы определяем ресурс, который уже выработан, определяем оставшийся ресурс и полный ресурс или срок работы по каждому из этих критериев.
При этом в расчетах используется специальная функция зависимости скорости изнашивания радиальных сопряжений от величины зазоров, которая была получена на основании решения задачи динамики износа ЭЦН и подтверждена опытным путем по результатам лабораторных исследований и послеэксплуатационного анализа.
Впервые в практике нефтедобывающей отрасли применен подход, позволяющий научно обоснованно определить конструкционную надежность насосов для конкретных условий эксплуатации.
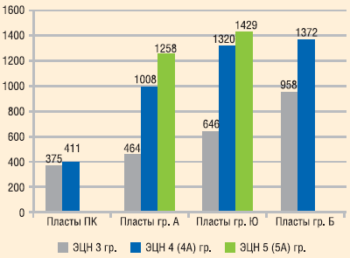
В ходе этой работы выполнена оценка технического ресурса насосных секций различных конструкций в условиях различных объектов разработки, которые показали существенные различия надежности ЭЦН различных групп в зависимости от эксплуатируемых пластов (рис. 10).
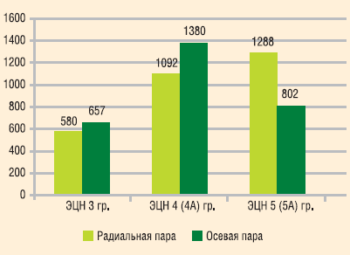
Для понимания общей картины проводилась оценка ресурса по критерию скорости износа радиальных и осевых сопряжений рабочих ступеней в зависимости от конструкции насоса по результатам всех измерений (рис. 11).
В результате был выявлен целый ряд вопросов, требующих дополнительных исследований. Например, в стендовых условиях ресурс как радиальных, так и осевых сопряжений ЭЦН 5 (5А) группы (пакетная сборка с осевыми подшипниками), превышал аналогичные показатели ЭЦН группы 4 (4А), однако в реальных пластовых условиях результат оказался неожиданным – теперь нам предстоит выяснить причины такого несоответствия.
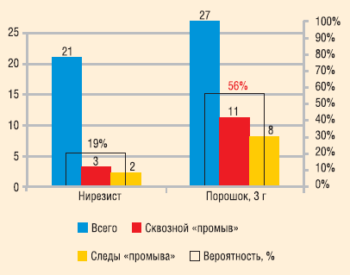
Эта же группа исследований дает оценку надежности ЭЦН по критерию «промыв» (рис. 12). Вероятность наступления отказа по критерию «промыв» у насосов с РО из обычных порошков в условиях пластов группы АВ составляет 56%, то есть этот материал не предназначен для эксплуатации в данных условиях. Нужно применять по крайней мере низколегированные порошковые материалы (группы 4А, 5А).
Таким образом, на основании полученных научных расчетов конструкционной надежности оборудования, анализа существующего и оптимального (целевого) распределения парка погружного оборудования по группам исполнения, можно с уверенностью говорить о реальности достижения среднего времени безотказной работы оборудования на уровне 650 суток и установлении новых целевых ориентиров показателей наработки на отказ на уровне 900–1000 суток.
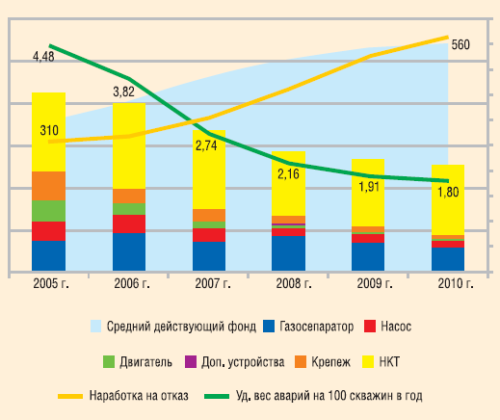
АНАЛИЗ И РЕШЕНИЕ ПРОБЛЕМ АВАРИЙНОСТИ УЭЦН
Повышая наработку на отказ УЭЦН, нельзя забывать о поиске решения проблемы аварийности УЭЦН. С увеличением продолжительности эксплуатации установок увеличивается и время негативного воздействия на детали коррозионно-абразивной жидкости, что приводит к накоплению усталостных и иных повреждений и повышает вероятность наступления аварии. Поэтому в деле снижения аварийности УЭЦН важно сработать на «упреждение», заранее предвидя и решая те проблемы, которые могут возникнуть с ростом наработки до 600 суток и более. В этом направлении мы также добились заметных успехов: значительно сократилось общее число «полетов», при этом действующий фонд скважин и среднее время работы УЭЦН увеличились. Удельный уровень аварийности УЭЦН на фонде ТНК-ВР за 2010 год сократился более чем в два раза по сравнению с количеством аварий за прежние годы. Снижение аварий достигнуто по таким узлам, как насос, двигатель, фланцево-болтовые соединения и крепеж, однако доля аварий по НКТ и газосепараторам по-прежнему остается высокой (рис. 13).
Снизить количество аварий удалось благодаря научно-исследовательской и конструкторской работе, проводимой ТНК-ВР совместно с ООО «ИМАШ ресурс» и заводами-изготовителями УЭЦН.
Мы также провели ряд экспериментов в РГУ нефти и газа им. И.М. Губкина, посвященных исследованию эффективности борьбы с газом различных устройств, которые показали, что на сегодняшний день альтернативы газосепаратору, к сожалению, нет. Поэтому необходимо кардинальное решение проблемы аварий по данному узлу УЭЦН.
К настоящему времени нами уже найдены конструктивные решения и предприняты соответствующие шаги по предотвращению аварий по нижнему основанию газосепараторов, связанных с усталостным изломом шеек и «промывом» зоны входных отверстий.
Анализ вышедших из строя газосепараторов показывает, что в течение последних двух лет основные разрушения происходят в районе средней части гильзы (корпуса), а также в местах стыков гильзы и корпусных деталей (рис. 14). Именно поэтому в 2010 году основной акцент проводимых научных работ был сделан на исследование этих проблем. В ходе этой работы была впервые разработана понятная модель отказа («промыв») и методика испытаний материалов.
В общем виде ресурс гильзы и корпуса газосепаратора определяется по формуле:
где h – толщина стенки корпуса и защитной гильзы;
V – скорость изнашивания:
V = f(pH, q, ωM, d, HB, Ka, Kэ),
где pH – водородный показатель (коррозионная активность среды); q – концентрация абразивных частиц; ωM – местная скорость; d – диаметр абразивных частиц; HB – твердость частиц; Ka – стойкость мате-
риала к гидроабразивному изнашиванию; Кэ – стойкость материала к коррозионно-эрозионному изнашиванию.
Отсюда следуют основные конструктивные меры по решению проблемы аварийности и увеличению ресурса газосепаратора по критерию «промыв». Это увеличение толщины стенки, снижение скорости потока путем изменения конструкции и повышение стойкости материала к гидроабразивному и коррозионно-эрозионному изнашиванию. В настоящее время продолжаются специальные исследования абразивно-коррозионно-эрозионных процессов, приводящих к «промыву», для оценки скорости изнашивания различных материалов и покрытий:
- твердые сплавы: ВК30, ВК15, ВК8, в том числе с нанодобавками – ВК8УДП (наименьшая скорость изнашивания);
- покрытия, полученные детонационным способом и по HVOF технологии: WC15, WC30, Nanostil, наноструктурированный порошок WC12;
- высокохромистый чугун, стали аустенитного класса 02Х18Н10Т, их зарубежные аналоги, сплав К-монель и т.д.
В ближайшем будущем результаты этих исследований будут учтены при выборе материалов и производстве погружного оборудования, и это станет далеко не последним примером сотрудничества ТНК-ВР, научно-исследовательских организаций, заводов-изготовителей оборудования. Такая совместная работа прекрасно зарекомендовала себя в рамках проекта по повышению наработки УЭЦН на отказ до 600 суток, и именно она станет залогом будущих достижений Компании в области эффективности механизированной добычи нефти.
Для отправки комментария вам необходимо авторизоваться.